Robot teleoperation is a vital technology enabling human operators to perform tasks in remote or hazardous environments with enhanced safety and precision. As communication and AI technologies evolve, teleoperated robots will become more responsive, autonomous, and capable of handling complex tasks with minimal latency and high accuracy.
IIT Robot Teleoperativo project, in collaboration with INAIL (“Istituto Nazionale per l’Assicurazione contro gli Infortuni sul Lavoro” – National Institute for Insurance against Workplace Injuries, Italy) CUP J32F17000950005, is aimed at the development of a novel, collaborative teleoperation hardware and software system dedicated to operating in certain hazard-prone industries, reducing the risks to the workers’ safety and well-being. It utilizes, develops, and integrates advanced technologies in tele-locomotion, tele-manipulation, and remote human-robot interaction.
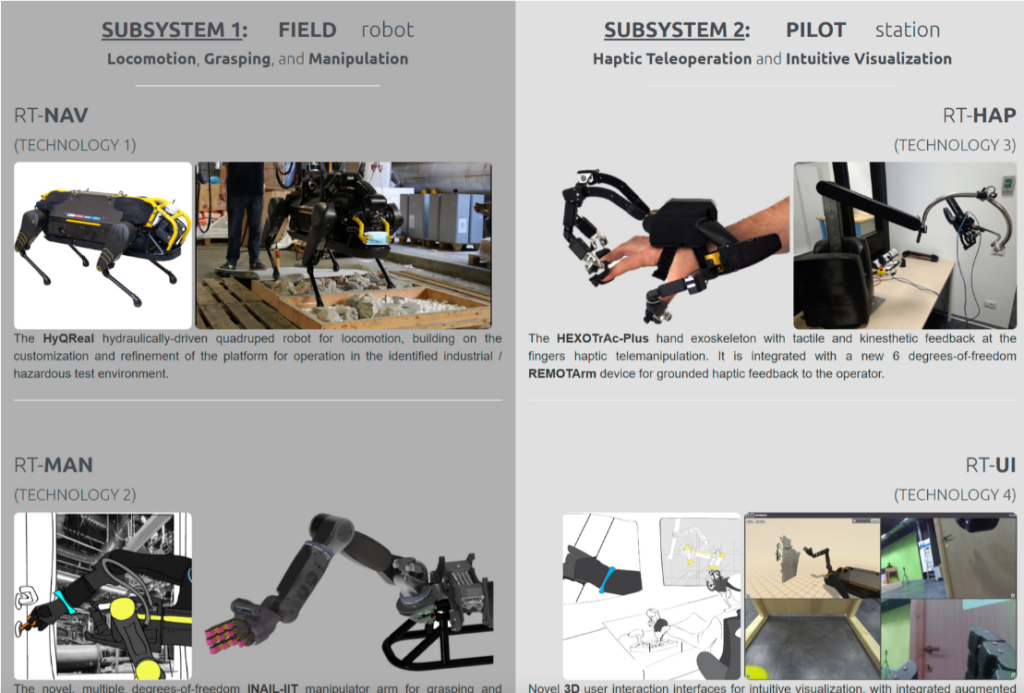
These systems are used in environments where direct human interaction is impractical or hazardous, such as deep-sea exploration, space missions, medical surgery, and hazardous material handling. Teleoperated robots allow operators to manipulate robotic systems with precision while receiving sensory feedback to enhance control.
Components of a Teleoperated Robot
A teleoperated robot typically consists of the following key components:
1. Master Controller
- The human operator uses a control device such as a joystick, haptic glove, or specialized interface to send commands to the robot.
- Advanced controllers incorporate haptic feedback to provide a realistic sense of touch and force.
2. Communication Link
- A robust communication channel is essential to transmit control signals and receive sensory feedback.
- Depending on the application, the communication link may use wired (Ethernet, fiber optics) or wireless (Wi-Fi, satellite, RF) technology.
3. Robot (Slave Unit)
- The physical robotic system that executes the operator’s commands.
- Can be mobile or stationary, equipped with arms, sensors, and end effectors for task execution.
4. Sensors and Feedback Mechanisms
- Cameras, LiDAR, and ultrasonic sensors provide visual and spatial feedback.
- Force and tactile sensors enhance precision, particularly in surgical and industrial applications.
Types of Teleoperated Robots
1. Direct Teleoperation
- Operator controls the robot in real-time with minimal automation.
- Used in bomb disposal, military reconnaissance, and hazardous material handling.
2. Supervised Teleoperation
- Operator provides high-level commands while the robot performs tasks autonomously.
- Applied in space missions, underwater exploration, and semi-autonomous surgical systems.
3. Haptic Teleoperation
- Incorporates force feedback to simulate touch and resistance.
- Commonly used in medical robotic surgery and remote industrial applications.
Challenges in Teleoperated Robotics
1. Latency and Communication Delays
- Signal delay affects real-time control, particularly in space or long-distance applications.
- Solutions include predictive modeling and AI-assisted control.
2. Precision and Stability
- High precision is necessary for applications such as surgery or micro-assembly.
- Advanced control algorithms and haptic feedback help improve accuracy.
3. Security and Reliability
- Protection against cyber threats is critical for remote-controlled systems.
- Encrypted communication and redundancy mechanisms enhance reliability.
Applications of Teleoperated Robots
1. Medical Field
- Robotic-assisted surgeries (e.g., Da Vinci Surgical System) allow remote specialists to perform delicate procedures.
2. Exploration
- Used in deep-sea and planetary exploration (e.g., NASA’s robotic arms on Mars rovers).
3. Industrial and Military Uses
- Bomb disposal robots, hazardous material handling, and remote welding in nuclear facilities.
4. Disaster Response
- Robots assist in search and rescue operations in areas unsafe for humans.
Future of Teleoperated Robotics
Advancements in AI, machine learning, and 5G communication will enhance the efficiency of teleoperated robots. Increased autonomy and real-time haptic feedback will further bridge the gap between human operators and remote robotic systems, expanding applications in critical fields such as medicine, space exploration, and industrial automation.
Remote robotic teleoperation is becoming vital in numerous fields, especially in hazardous environments where human safety is critical. In these scenarios, teleoperated robots are deployed to perform tasks, reducing human exposure to potential dangers. The “Robot Teleoperativo” project aimed
to develop a novel, collaborative teleoperation hardware and software system dedicated to operating in hazard-prone environments, reducing risks to people’s safety and well-being.
It employed, developed, and integrated advanced technologies in tele-locomotion, tele-manipulation, and remote human-robot interaction. This short paper provides an overview of the latest
developments in the project and a preliminary system evaluation. The project has successfully demonstrated a teleoperation system that enables intuitive and immersive tele-locomotion,
tele-manipulation, and remote human-robot interaction.
The project showcases the potential for enhanced operator control and precision, offering a more natural and effective means of remote interaction in complex and hazardous environments.
The Approach
The project is built on FOUR key technologies, divided into TWO overall subsystems, as described below. The simultaneous research and exploitation possibilities in the technologies drive the contributions in the project. Below the technologies and their main features – the FIELD robot composed of the INAIL-IIT Robotic Arm and the HyQReal hydraulic quadruped platform; and the PILOT station composed of the REMOTArm + HEXOTrAc-Plus teleoperation platform, combined with the 3D immersive VR visualization interface.
