Japanese design firm Serendix has automated process to build scalable 3D-printed housing pod that takes less than a day to create at very affordable cost.
Serendix, which hopes to make housing more affordable, recently combined 3D printing and CNC machining to build a house for very affordable cost.
Serendix Corporation (Headquarters: Nishinomiya City, Hyogo Prefecture; President: Hiroyasu Koma) announces the completion of serendix50, Japan’s first 3D printed housing for two-person households, in Komaki City, Aichi Prefecture.
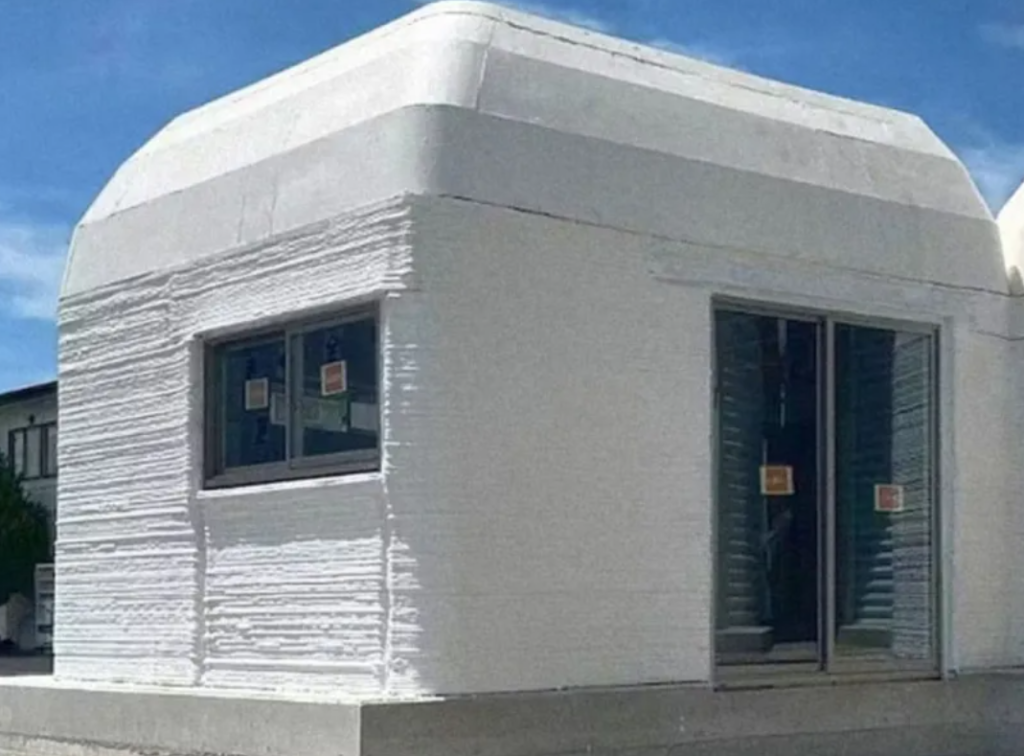
Serendix has five printers, according to Peters, each of which can construct 50 houses per year, and the company intends to add more in 2024 in order to reach a goal of 850 per year.
The serendix50 (Fujitsubo model) was developed by the Keio University KGRI Center for Design and Digital Manufacturing in response to the many requests from couples in their 60s and older for a 3D printer house for their final home. (Representative: Hiroya Tanaka, Professor at Keio University SFC) as a joint project. (headquartered in Kumamoto Prefecture), Hyakunen Housing Corporation (headquartered in Shizuoka Prefecture), and Nabeju Corporation (headquartered in Gunma Prefecture), and was completed in just 44 hours and 30 minutes.
Handa added that the company’s goal is to fully automate the housing industry — much like Japan did with the auto industry more than 40 years ago.
serendix50 (Fujitsubo model) details
Structure :Steel frame + reinforced concrete, flat roof
Housing development entity : serendix
Outline design and concept : Keio University KGRI KAN Design & Digital Manufacturing Creation Center
Execution Design : Eimu Masuyam (Associate Professor, University of Miyagi, Senior Research Fellow, Keio Research Institute at SFC, Keio University)
Structural Design: KAP Inc.
Total floor area : 50m2
Maximum height : 4m
Location : Komaki City, Aichi Prefecture, Japan
Estimated sales price : 5.5 million yen
Serendix Inc had joined hands with a world-leading expert in 3D printing technology, Hiroya Tanaka (professor of Keio University), to build a house for the general public.
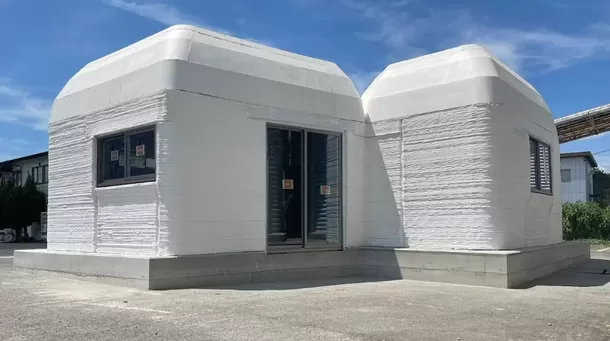
Serendix utilized concrete to print the walls of its 538-square-foot “barnacle” unit, giving an individual or a couple a bit of extra stretching room than a typical 100- to 400-square foot tiny house.
3D printing has been around since the 1980s, when Dr. Hideo Kodama created a machine that hardened material with UV light
3D-printed house only took 44 hours and 30 minutes to build. The efficiency of the construction time means that negative environmental impact is reduced