Architecture studio Grimshaw and the University of East London have collaborated to create Sugarcrete, a biomaterial construction block with an interlocking shape made from the sugarcane by-product bagasse. Sugarcrete was developed to be a low-cost and low-carbon reusable construction-material alternative to brick and concrete.
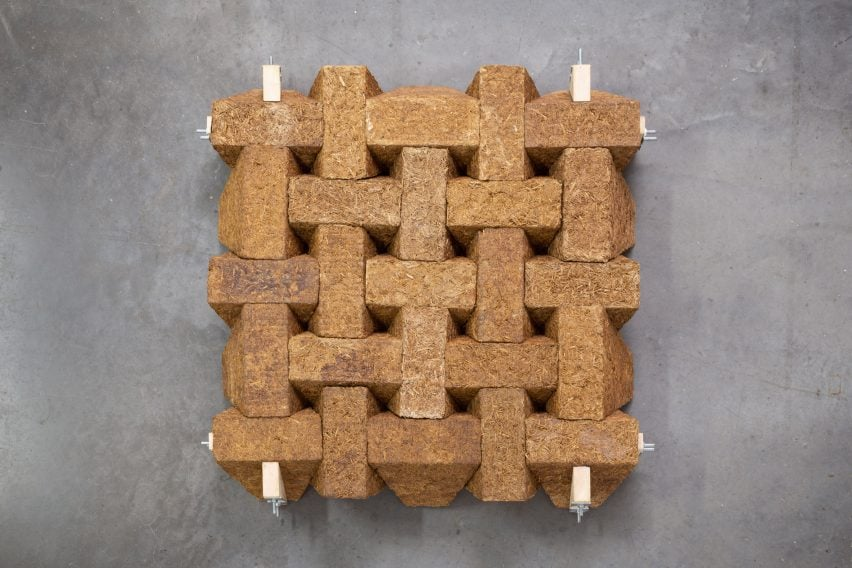
The Sugarcrete TM project brings together experts from the University of East London and sector leading organisations Grimshaw and Tate & Lyle Sugars to co-create ideas and offer viable construction solutions for real world applications, using bio-waste as the core resource.
The project has been developed as a collaboration between the MArch Architecture programme and the Sustainability Research Institute (SRI) by Armor Gutierrez Rivas, Senior Lecturer in Architecture; Alan Chandler, Dean of Research and Bamdad Ayati, SRI Research Fellow, with partners Elena Shilova, Grimshaw Architects, and John Kerr, Vice President of Research & Technology, Tate & Lyle Sugars.

Project Aims
The aim of the project is to develop ultra-low carbon building components using sugarcane bio-waste (bagasse), allowing the storage of biogenic carbon from fast-growing plants in construction materials as an effective strategy to delay carbon emissions.

Project Details
Sugarcane is the world’s largest crop by production volume. The processing of sugarcane to produce sugar, generates enough products to entirely replace high energy-demanding construction systems such as concrete or brick. Sugarcane growth provides one of the fastest CO2-to-biomass conversion mediums available, up to 50 times more efficient than forestry.
Research developed at UEL demonstrates how this waste stream can provide a sustainable construction material. The new Sugarcrete TM material, prototyped using advanced digital modelling and robotic fabrication, presents high-quality mechanical, acoustic, fire and thermal properties, and has been tested to industry standards for fire resistance (ISO 1716:2021), compressive strength (ASTM C39), thermal conductivity (Hot-Box method) and durability (BS EN 927-6), carried out at UEL by the research team in the Sustainability Research Institute (SRI) facilities. The testing has shown promising results for Sugarcrete TM to be used use as insulation panels, lightweight blocks, load bearing blockwork and structural floor and roof slabs.
Grimshaw’s interest in interlocking geometries has brought new opportunities to deploy Sugarcrete TM as a spanning element to construct a demountable, reusable, fire resistant composite floor slab called Sugarcrete TM Slab a one of a series of prototypes developing innovative construction applications which can be applied, disassembled, or extended in new or existing structures.
Sugarcrete TM Slab adapts Abeille’s 1699 design for dry assembly flat vaults – the system is made of interlocking components which transfer loads across the slab between blocks, restrained using post-tensioned perimeter ties, reducing the steel content of the slab up to 90 per cent. Reducing steel, combined with the use of sugar cane fibres of different densities in a modular system allows the slab assembly to avoid the potential risks of cracking which occur with traditional concrete in extreme situations, absorbing the effects of seismic shock – a characteristic vital in earthquake prone regions where sugar cane is cultivated.
Prototype testing conducted at UEL’s SRI laboratories shows that Sugarcrete TM Slab can offer an alternative to concrete slabs while demonstrating exemplary environmental benefits including carbon emissions 20 times lower than traditional concrete. The system also minimises curing time to one week compared to standard concrete which takes at least 28 days, it is five times lighter than concrete, and is substantially cheaper compared to concrete production.
Upcycling bagasse could help develop locally made construction solutions for sugar producing communities in the global South where construction materials are frequently imported, environmentally poor performing, high cost and high carbon – for example a concrete block in Cuba, a major sugar producing country costs $3 – an average monthly salary is $148.
The project partners are identifying sites in the sugar producing Global South where the Sugarcrete TM Slab prototype will next be tested in collaboration with local NGOs. Key to the research is to develop a technology and production outcome that uses sugar cane bio-waste in its local context – minimising transportation costs for local producers allows localised production to make radically new, affordable and ultra-low carbon ‘vernacular’ building materials that can create new income streams via export to the Global North.